
State of the Art

Digital Fabrication
Digital fabrication is commonly defined as “a fabrication or building process driven by the seamless conversion of design and engineering data into fabrication code for digitally controlled tools” (Kaseman and Graser 2020; Gershenfeld 2012). It is a way of fabricating physical products using computer-controlled tools and machines. There are many types of digital fabrication tools, popular ones being computer numerical controlled (CNC) routers and mills, laser cutters, and 3D printers.
Digital fabrication can be split into two main categories, subtractive manufacturing (SM) and additive manufacturing (AM). Subtractive manufacturing is the process of removing material from a workpiece. Think of it as carving the product from a piece of wood, you remove material until you are left with the piece you desire. Various cutting and shaping tools are used for subtractive manufacturing like CNC routers and lasers. Additive manufacturing is the opposite of subtractive manufacturing, here you add material until you have the product, like combining LEGO blocks to create a finished model. The various methods of 3D printing are considered additive manufacturing tools. Machines can combine the two methods of digital fabrication into hybrid manufacturing (HM) systems, which contains tools from both additive and subtractive manufacturing.
Both subtractive and additive manufacturing tools are generally mounted on either linear robots or articulated robots. Linear robots, often called gantry robots after the gantry cranes they resemble, consist of a frame with linear rails with the tool mounted at the top, facing downwards. This allows the machine to move the tool left and right (X-axis), forward and backwards (Y-axis), and up and down (Z-axis) to reach every spot inside its build volume. Because of the top mounted tool, it is limited to work from the bottom and up, it cannot rotate or go beneath the product it is working on. Articulated robots, often called robot arms or industrial robots, feature a series of rotational joints allowing them to manipulate the attached tool to a higher degree. They can be stationary, attached to rails, have tracks so they can move around freely, or even be attached to linear robots in combined systems. While they are limited by the reach of the robotic arm, they have the ability to rotate to work on a product from multiple directions. The different types of robots have their advantages and disadvantages, linear robots are well-suited for working on or creating large objects, typically operating at faster speeds, with less vibration, and a larger work area. They are, however, usually a lot bigger and heavier than their articulated counterparts, requiring more resources and equipment to move and install as well as being less flexible in terms of object orientation and more complex geometries.

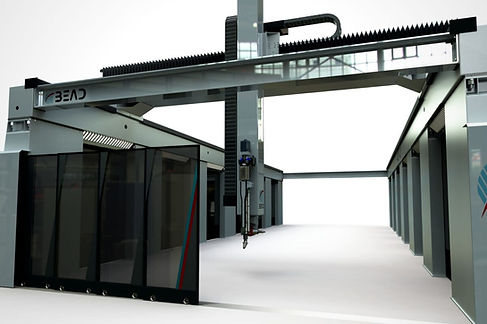
A CEAD AM Flexbot articulated robot (left) and BEAD linear robot (right), both are able to mount both a 3D printing head (additive manufacturing) and milling tools (subtractive manufacturing).
Common to both types of digital fabrication is the use of computer software to design and process the product. Typically, a computer-aided design (CAD) software application is used to create a digital representation of the product, establishing the dimensions and features necessary. Common CAD programs in the AEC industry are building information modeling (BIM) packages like ArchiCAD or Revit, as well as 3D modelling software applications like Rhinoceros3D, AutoCAD, and SketchUp. Once the product has been created digitally, it needs to be processed for manufacturing using a computer-aided manufacturing (CAM) software application. The CAM software is used to check for errors in the model and to create toolpaths that convert the digital representation of the product into machine language that instructs the automated tool how to create the product physically. The most common machine language for digital manufacturing is called G-code, which was developed at MIT in the 1950s.
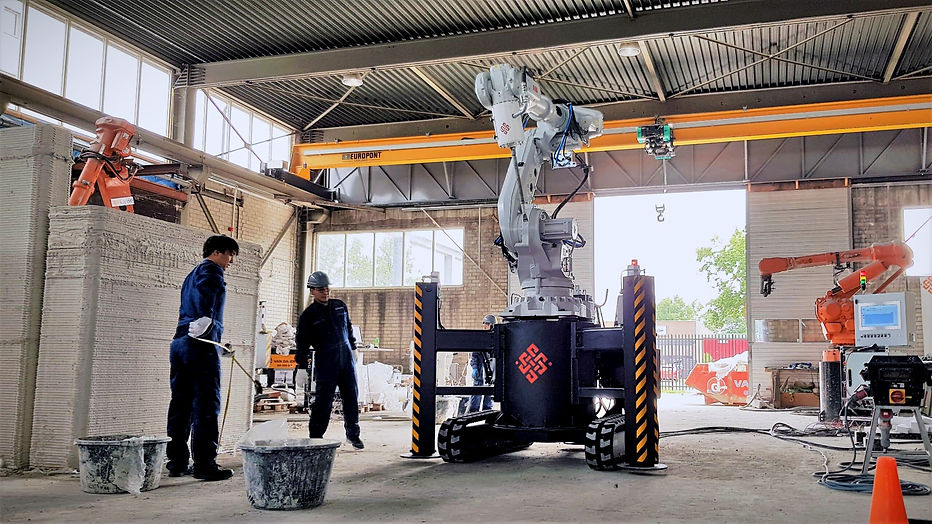
The CyBe Robot Crawler is 3D printer mounted on tracks able to move around and work on-site as well as in a factory setting. The tracks enable it to work in various conditions and terrain, and the hydraulic feet allow it to stabilize as well as increase its reach. The articulated robot arm makes the printer able to reach hard to get to places, as well as manipulate the printing tool to produce complex shapes and textures. The printer can print up to 500 millimeters per second with CyBe's proprietary mortar which sets in only 3 minutes.
Subtractive Manufacturing
Subtractive manufacturing is based on the principles humans have been using to create objects throughout history, by carving a block of material to create everything from tools to pieces of art. Using a wide variety of machines and tools it is now possible to cut products from all kinds of materials, including, but not limited to, wood, metal, plastic, stone, ceramics, glass, and various composites. Common tools for cutting, engraving, and shaping are different drill bits and blades typically used in routers and mills, laser cutters which use a high-powered laser source to vaporize material, waterjet cutters that use a jet of high-pressure water, sometimes combined with an abrasive like garnet or glass, and flame cutters which use fuel gasses combined with pure oxygen.
There are advantages and disadvantages to the various methods of subtractive manufacturing. A laser cutter, for example, is usually able to work at a lot higher speeds than a CNC router but is best suited to cutting thinner pieces of material. A CNC router requires the work piece or material to be restrained, either through clamps, screws, glue, or a dedicated vacuum table. On the other hand, the laser cutter requires the material to not be as egregiously fastened, often requiring no restraints or just simple tape. The CNC is able to cut out complicated three-dimensional shapes that laser cutters are not able to because of their shallower cutting depth. Digital files are easier to prepare for machines working in 2D, like most laser cutters, than ones working in 3D. Waterjets work similarly to laser cutters but leave no burn marks, but they cannot engrave like the lasers and typically require more maintenance and cleanup. Subtractive manufacturing tools are usually used to create products within a factory or workshop setting.

The Shinjuku Miyabi Residence by Himematsu Architecture. The Tokyo hotel features a backlit laser cut facade with a stylized hemp leaf asa no ha pattern. Common on children's clothing, the asa no ha pattern represents growth, as the hemp plant grows up to four meters in four months.
Tverrfjellhytta, the Norwegian Wild Reindeer Pavilion, by Snøhetta features an organic wooden core CNC milled out of pine timber beams to give the impression that it has been shaped by eroding natural forces like wind and running water. The soft core is designed to provide a warm gathering place as a contrast to the protective rigid frame of steel and glass. Images by Ken Schluchtmann & Ketil Jacobsen.
Additive Manufacturing
Additive manufacturing, as the term implies, is a fabrication method where material is added bit by bit to create the finished product. The most common additive manufacturing method is 3D printing. A wide variety of technologies within 3D printing exist. For the most part they work by building products by adding material layer by layer, typically by either extruding a semi-liquid material through a nozzle or by solidifying a liquid or powdered material with a laser or additive. The different types of 3D printing can create products in a wide variety of materials like concrete, sandstone, glass, stainless steel, aluminum, titanium, clay, sand, ceramics, porcelain, plaster, gypsum, resin polymers, biopolymers and more. Depending on the technology, 3D printers can be used on-site, in factories, or both.
Fused Deposition Modeling
The most common type of 3D printer is the fused deposition modeling (FDM) printers. Simple in the way they work and popular among private consumers, you will find these dotting the various makerspaces and workshops around the globe. FDM printers work by extruding a material, typically heated plastic polymers in the small consumer versions, onto a surface called the build plate. For example, they can be used to 3D print dissolvable formwork that is extremely light and could be quickly assembled on the site. In the AEC industry, concrete 3D printers are the most common type of FDM printers. Contrary to regular concrete, which is cast in formwork or molds, concrete 3D printers extrude layers of wet concrete that are typically 2 to 10 centimeters wide. This uses significantly less material than traditional methods and provides hollow areas that can be filled with insulation or fitted with ducts for electrical systems or ventilation. The structure can be reinforced by adding various fibers like polypropylene, steel, or glass to the concrete mixture. The hollows can be fitted with rebar, and traditional concrete can be poured into them to reinforce the structure. While a concrete 3D printer typically extrudes a rounded line, resulting in a striped look to the printed result, the printer can be equipped with side flaps and a tangential nozzle, which rotates to match the print direction, providing a smoother end product. Concrete 3D printers come in various sizes and forms, both on linear robots, called gantry printers, and articulated robots.

3D printed capital for the reconstruction of the Monumental Arch of Palmyra, an ancient Roman ornamental archway from the 3rd century BC that was destroyed by ISIS in 2015. Printed in climate friendly stone material by the Dutch company CONCR3DE using Binder Jetting.
The BOD2 is a modular gantry printer produced by the Danish company COBOD. It can be installed on-site and has a printing volume of up to 14.5 meters wide and 8.1 meters tall with no limit to length. It only requires two people to operate after installation and is able to print the walls of a 100 m2 in 14-15 hours of print time (not counting preparation and cleaning time). The BOD2 system was recently used to 3D print a 3-story villa, the tallest on-site printed building in the world.
Striatus, a 3D printed concrete bridge created by the Block Research Group (BRG) at ETH Zurich and Zaha Hadid Architects Computation and Design Group (ZHACODE), in collaboration with incremental3D (in3D) and building material manufacturer Holcim.
Direct Energy Deposition
Another form of additive manufacturing is Directed Energy Deposition (DED), which is often compared to welding. During the DED process, materials are deposited as they are melted by utilizing thermal energy, causing the materials to fuse. There are multiple categories of directed energy deposition, depending on whether the material is in the form of powder or a wire, as well as on the heat source (Ahn 2021). In Wire Arc Additive Manufacturing (WAAM), an electric arc is used to generate heat (Xia et al. 2020).
MX3D used Wire Arc Additive Manufacturing (WAAM) technology to 3D print a 12 meter long stainless steel pedestrian bridge placed in the oldest district of Amsterdam. The bridge is equipped with sensors creating a digital twin by monitoring strain, displacement, vibration, how many people are crossing it, how fast they are moving, as well as local air quality and temperature in real time. This allows the engineers to measure its health and how it changes over its lifespan. Autodesk, The Alan Turing Institute, and the Amsterdam Institute for Advanced Metropolitan Solutions (AMS) were partners in the project.
Binder Jetting and Selective Laser Sintering
Binder jetting is a 3D printing process that shares similarities with regular 2D ink printers. In this process, a powdered material is solidified using chemical binding agents (Shakor et al. 2022). First, a thin layer of powder is added on a build platform. The printer then selectively adds the binding agent through a nozzle, fusing the powder particles together in specific areas according to the digital file. Layers of powder are repeatedly added and solidified until the object is complete. Binder jetting can be used with a wide range of materials, including gypsum, cement, clay, chipped wood/cellulose, and quarts-sand. It is considered to be the fastest additive manufacturing method for creating a large volume of complex shapes. Selective Laser Sintering (SLS) is a similar method, here the layers of powder are fused together through the use of a laser instead of chemical binder.
Gothic Reimagined, a collaboration between designers Dustin White and Christopher Pope and the 3D printing company CONCR3DE. The generative text-to-image artificial intelligence model Midjourney was used to reinterpret gothic style. The resulting image was then developed into a 3D relief model and printed with CONCR3DE's Armadillo 3D printer in limestone from recycled materials.
Advantages
There are several advantages that digital fabrication methods provide compared to traditional manufacturing. While all of these advantages are not universal to every type of digital fabrication, different types can be used in concert to improve the design and construction process overall.
Customization
One of the main advantages of digital fabrication is its ability to create geometrically complex custom forms with intricate detail that is difficult or impossible to produce using traditional manufacturing methods. This allows for increased freedom when it comes to aesthetics, as the method of production is subject to less restrictions. Elements can be topologically optimized to reduce size and weight, which in turn reduces costs. Other building components can be integrated into the elements because of the custom nature of the components, allowing for a more holistic approach to design.
Accuracy and Precision
The machines and robots used in digital fabrication are designed to manufacture components with a high level of accuracy and repeatability. They follow the digital design provided to it exactly as provided without deviation. The end result is therefore more reliable and precise than what a human laborer would produce.
Efficiency and Safety
Digital fabrication methods reduce the laborers required while increasing speed. The machines usually require between one to four operators and are able to produce components that traditionally would require a lot more workers. They also work at a faster pace. The increased reach of the robots allows them to perform dangerous work at heights, requiring less cranes and scaffolding. They can also manipulate dangerous equipment like welding torches and saws with less risk of injury.
Digitalization
Because of the digital nature of the workflow, buildings produced for digital fabrication are easily integrated with other digital systems. Simulations can be done on environmental and energy factors, life-cycle assessments and costs, usage patterns and more. Sensor technology can be used to create various smart solutions to improve the functionality and usage of the building. Virtual reality allows the designer and clients to experience the design before construction, and augmented reality can provide the contractors with enhanced instruction and overview in the construction phase.

3D printed concrete pad foundations (right) optimized to use 75 % less material compared to traditionally built concrete foundations (left). Developed by Hyperion Robotics in collaboration with Peikko for Iberdrola.
Challenges
Standards and Certifications
Building components are rigorously tested to make sure they uphold established standards and receive certifications in regard to relevant structural, safety, health, or environmental regulations. Elements created using digital fabrication can be bespoke in nature and will therefore have to go through compliance testing to make sure they uphold the same standards as traditionally manufactured products. Until standards and tools take into account the way digital fabrication methods produce customized solutions, some digital fabrication solutions might be expensive to test.
Digital Competency
At the moment, creating the files necessary for digital fabrication requires a higher level of competency than the current baseline of architects and designers. While the designs themselves can be made using traditional methods, like software that the architect prefers or even pen and paper, converting those to a format that can be sent to the fabricators is often left to specialists.
Industry Scaling
For digital fabrication to be viable in large projects, it has to be able to produce enough products to meet the demand in the projects. If a project requires one thousand elements, but there is only one machine available that produces one element per day, it is not a feasible option. Production has to reach a certain threshold before it can be considered viable for adoption. In the architecture, engineering, and construction industry, which traditionally has been slow to adopt new technology, this is a challenge.
Use in the AEC Industry
While the application of digital fabrication has not gained the same level of traction in the architecture, engineering, and construction industry as other industries, there are many promising examples that highlight the possibilities that the new technologies provide. In this section a selection of interesting projects that demonstrate various aspects of digital fabrication follows.
The HiRes Concrete slab created by the Digital Building Technologies team at ETH Zürich demonstrates various advantages of the application of 3D printing formwork for in-situ casting. In addition to being an aesthetically pleasing structural element that improves the spatial and acoustic qualities of the room, it also has integrated heating and cooling functionalities. Furthermore, by selectively placing material, the manufacturing method resulted in a 70 % reduction in material use compared to a traditional reinforced concrete slab.
An example of how digital fabrication can be used to build more sustainably is the Ashen Cabin by HANNAH. Wood from ash trees that is infested by emerald ash borer beetles would normally be rendered useless and classified as waste wood, due to the difficult shapes of the parts that remain after removing the damage. However, through the use of 3D scanning and digital fabrication methods, HANNAH was able to upcycle material that would otherwise be thrown away and create the Ashen Cabin, which stands on 3D printed concrete formwork.
The DFAB HOUSE is a collaborative project by the Swiss National Centre of Competence in Research Digital Fabrication and several industry experts and planning professionals. The project demonstrates different types of digital fabrication methods in one building. The main load-bearing element of the DFAB House is the Mesh Mould wall, an undulating concrete wall created using the In situ Fabricator (IF), a context-aware mobile on-site construction robot. The IF created the structure of the 12-meter-long double curved Mesh Mould wall by bending and welding 6 mm rebar into a 3D mesh. This steel mesh then served as both formwork and reinforcement for the wall. Concrete was poured and troweled by hand. This formwork would be extremely labor, cost and waste-intensive if created using traditional methods. The Mesh Mould wall supports the 78 square meter Smart Slab, a prefabricated concrete slab cast in 3D printed formwork. The geometrically optimized slab weights 15 tons, 70 % less than a conventional concrete slab, and cantilevers from the S-shaped wall supporting it. Smart Dynamic Casting (SDC) was used to create the window mullions, which allows for the creation of slender optimized load-bearing concrete elements. The upper floors were created using Spatial Timber Assemblies, a process where robots are used to create timer frame modules quickly and precisely. This system of using robots to create timber frames allows for an increase in complexity while enabling faster assembly on the construction site. The frames have no need for stiffening plates and thus allows the lightweight translucent facade, an aerogel-based translucent facade with ultra-high thermal insulation performance.
3D printing is not limited to structural components, but can also be used for producing technical elements. Systems Reef 2 (SR2) is an innovative 3D printed air-diffusion system, made from recycled plastic. Today’s air distribution systems are generic and have components with properties that are based on design tools and the manufacturing process of steel. However, SR2 has a form and layout that is inspired by nature and is highly optimized for air transportation. The result is that SR2 reduces length by 33 %, significantly reducing the number of fixings required and thus also the time and work it takes to install the system. The weight and cross-sectional area are reduced as well, resulting in reductions in embodied carbon and operational energy.